Învăța metoda Lean de a “rezolvarea problemelor”
Rezolvarea problemelor este nucleul sistemului de management Lean.
Toate instrumentele sistemului Lean sunt concepute pentru a identifica problemele. Aveți expertiza și standardizarea pe toate nivelurile organizației dvs. pentru a le rezolva?
Nivelul implicării și antrenamentului pe care îl are organizația dvs. în rezolvarea problemelor, va determina succesul și menținerea excelenței operaționale.

PUBLIC ȚINTĂ:
Senior Leadership, Functional Managers( HR, Finance, Sales..), Project Managers, Operations Managers, Lean Practitioners,
DURATA CURSULUI
Lean systematic Problem Solving – 8 Hours (1 Sessions)
Gemba real time Problem Solving – 16 Hours (2 Sessions)
Introducerea în “Rezolvarea problemelor”
RECOMANDAT INDUSTRIILOR:
All kind of companies, Manufacturing & Services
LOCURI LIMITATE:
6 teams (30 participants)
INSTRUCTOR

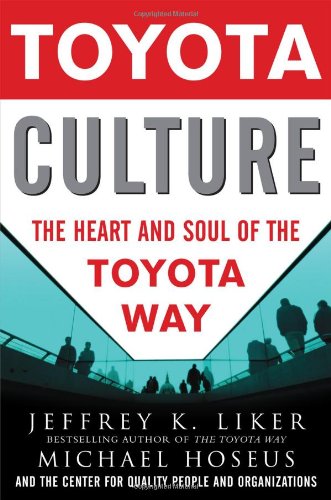
MICHAEL HOSEUS
- Executive Director for the Center for Quality People & Organizations (CQPO). Mike Hoseus brings both manufacturing operations and specialization in Human Resource experience to CQPO. CQPO is an organization developed in 1999. Current projects with Toyota include New Hire selection and training process, Team Leader and Group Leader post promotion training, Quality Circle Leader and Manager training, and Global Problem Solving for all levels.
- Adjunct professor with the University of Kentucky’s Lean Manufacturing Program.
- Co author with Dr. Jeffery Liker (Author of the Toyota Way) of Toyota Culture.
- Adjunct professor with the University of Kentucky’s Center for Manufacturing and a member of the faculty of Lean Enterprise Institute.
- Corporate leader for 13 years at Toyota Motor Manufacturing’s Georgetown, Kentucky, plant both in Human Resources and Manufacturing.
- Assistant General Manager in Human Resources, his responsibilities included personnel, safety, HR development, employee relations, benefits, training, and manufacturing/human resource teams for a plant of 8000 team members. His major initiative was development of the enhanced relationship between Human Resource and Manufacturing.
- In 1987 as a front line supervisor in vehicle assembly. This included all aspects of safety, quality, productivity, cost and morale for operations.
- With experience as Assembly Plant Manager and eventually Assistant General Manager, his responsibilities increased to include both assembly plants including operations, maintenance, and engineering.
- Certified Trainer in Global Problem Solving & Waste Reduction, Standardized Work and Kaizen Events.
TRAINING AGENDA: BODY OF KNOWLEDGE
Gemba “Real Time” Problem Solving Workshop – Two day course content
A continuation of the “Lean Systematic Problem Solving” workshop, this workshop gives participants and chance to practice the 8 Step method using real problems in a team setting with a coaching provided throughout the process.
This Workshop is intended for a very small audience, 30 maximum participants to be held at Hammond Power Solutions. Workshop attendees must also attend the Lean Systematic Problem Solving Session.
Lean Principles
- Origins of the Lean System (TPS)
- Lean Thinking objectives
- Lean at Transactional Environments
- Lean System vs. Traditional System
- Challenges in the Transactional Areas
- The 8 Wastes at the Office
- Definition of Value at Transactional Work
Module Activities/Exercises
- Value Classification (VA, NVA, BVA)
- 8 Wastes Walk
Transactional Process Indicators
- Process time, Lead Time , VAT
- Set ups, batch size & Fiability
- Inventory (Work in Process or in Queue)
- Accurate & Complete Info (%A&C).
- Information Technologies Used
- People Involved in the Process
Value Stream Mapping
- Document Information & customer requirements
- Identify Main Process es (In order).
- Select process indicators
- Walk the Value stream & draft main processes
- Identify how work is prioritized
- Calculate Value stream Metrics
Module Activities/Exercises
- Value Stream Case Mapple Inc.
- Value Stream Case Borgis Corp
Stability for Processes
- 5S & Visual Management
- Standard Work System
Flexiblity for Processes
- Pull Systems
- ContinuousFlow Approaches
Value Stream Improvement
- Value Stream Analysis & Proposal
- Consensus & Commitment in Action Plan
- Value Stream Mapping Future State
- Basic Problem Solving – PDCA Cycle
Lean sustainability
- KPI establishment
- Daily Management
- Cultural Enablers
- Lean Thinking vs. The Toyota Way
Follow up Application
- Explanation of the Post training activities
READ MORE ABOUT LEAN OFFICE
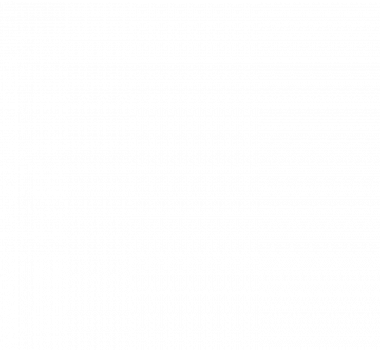